Energy-Saving Tips for Operating Forklifts
In today's fast-paced warehouse and industrial environments, energy efficiency is no longer just a sustainability goal — it's a competitive advantage. Forklifts, essential to most material handling operations, can be a significant source of energy consumption if not operated thoughtfully.
Whether you're managing a fleet of electric or internal combustion (IC) forklifts, adopting innovative energy-saving practices can significantly reduce operational costs while contributing to environmental responsibility.
Below are some proven energy-saving tips for operating forklifts more efficiently, drawn from industry best practices and real-world results.
Choose the Right Forklift for the Job
Efficiency starts with equipment selection. Using an oversized or underpowered forklift can waste fuel or battery life.
For example, deploying a 10,000-lb capacity forklift for tasks requiring only 3,000 lbs of lift is both unnecessary and inefficient.
Tip: Match the forklift's capacity, size, and power source (electric, diesel, propane, etc.) to the specific tasks and layout of your facility. Electric forklifts, in particular, are ideal for indoor operations due to their lower emissions and energy costs.
Maintain Proper Tire Inflation and Condition
Just like with cars, under-inflated or worn tires increase rolling resistance, forcing forklifts to work harder and consume more energy or fuel.
Poor tire maintenance also contributes to operator fatigue and reduced handling performance.
Tip: Regularly check and maintain tire pressure and replace worn tires promptly. Consider energy-efficient tire options like solid or cushion tires for indoor use.
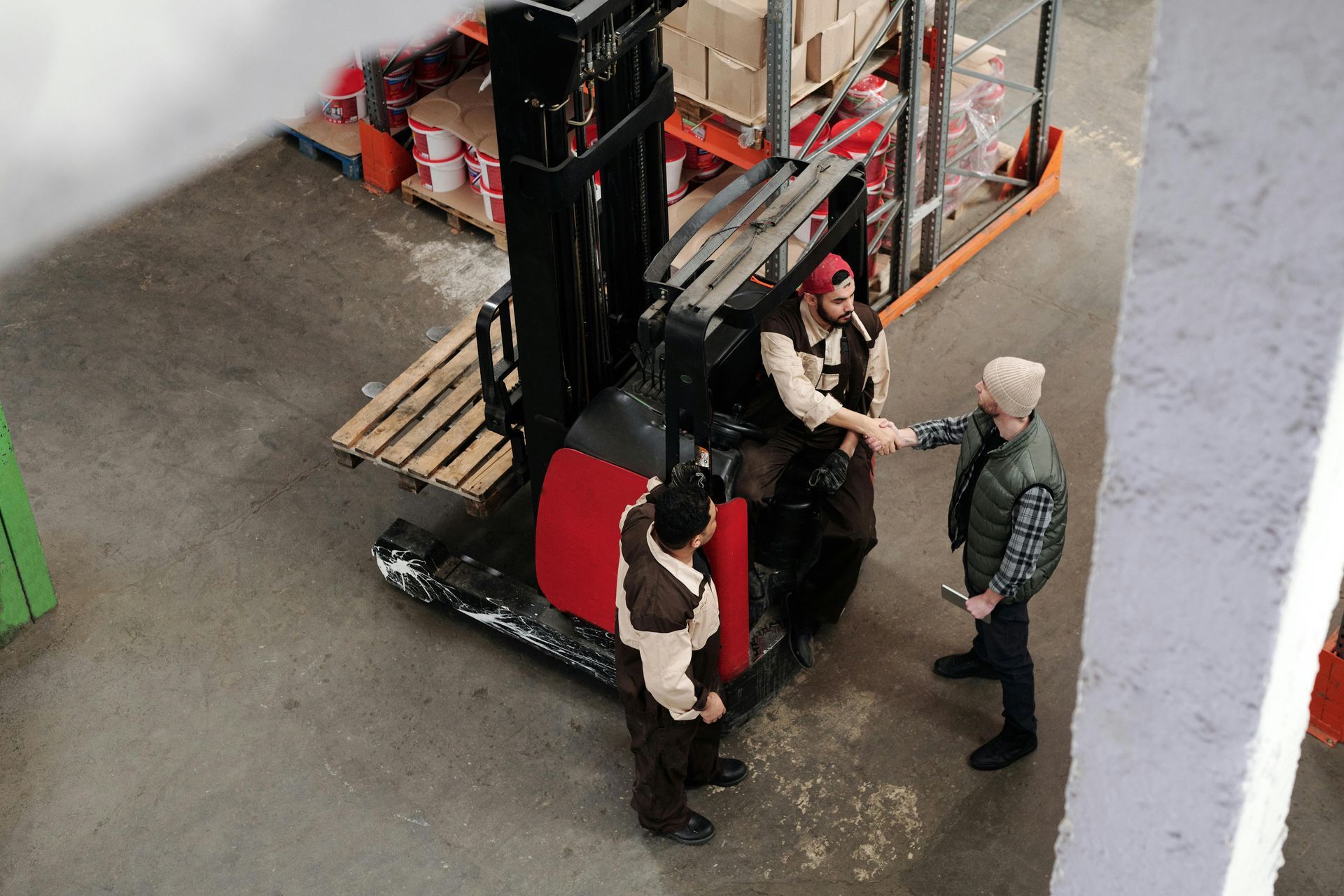
Reduce Idling Time
Many operators leave forklifts idling while loading, waiting, or on break. This seemingly minor habit adds up quickly, especially for IC forklifts, which burn fuel even when idle.
Even electric forklifts draw power while idling, reducing battery life and efficiency.
Tip: Implement a "no idling" policy. Encourage operators to shut down equipment during prolonged stops or downtime.
Schedule Preventive Maintenance
Well-maintained forklifts run more efficiently. Dirty air filters, old spark plugs, leaky hydraulics, and degraded batteries all increase energy use.
Regular servicing ensures peak performance, reduces breakdowns, and extends equipment lifespan.
Tip: Develop a preventive maintenance schedule based on manufacturer recommendations and usage patterns. Partner with certified service technicians to ensure quality work using OEM parts.
Train Operators on Energy-Efficient Techniques
Operator behavior is one of the biggest variables in forklift energy consumption. Excessive acceleration, hard braking, unnecessary revving, and inefficient route selection all burn extra energy.
Tip: Offer regular operator training that includes energy-saving techniques.
- Smooth acceleration and deceleration
- Using lower speeds when appropriate
- Avoiding carrying excessive loads
- Minimizing travel distances through better planning
Implement Smart Charging Practices (For Electric Forklifts)
Charging behavior has a direct impact on the lifespan and energy costs of electric forklift batteries. Opportunistic or partial charging can degrade batteries over time and increase energy consumption.
Tip: Use scheduled, complete charging cycles whenever possible and avoid letting batteries fully deplete. If available, invest in smart chargers or fleet management software that automates and optimizes charging during off-peak energy hours.
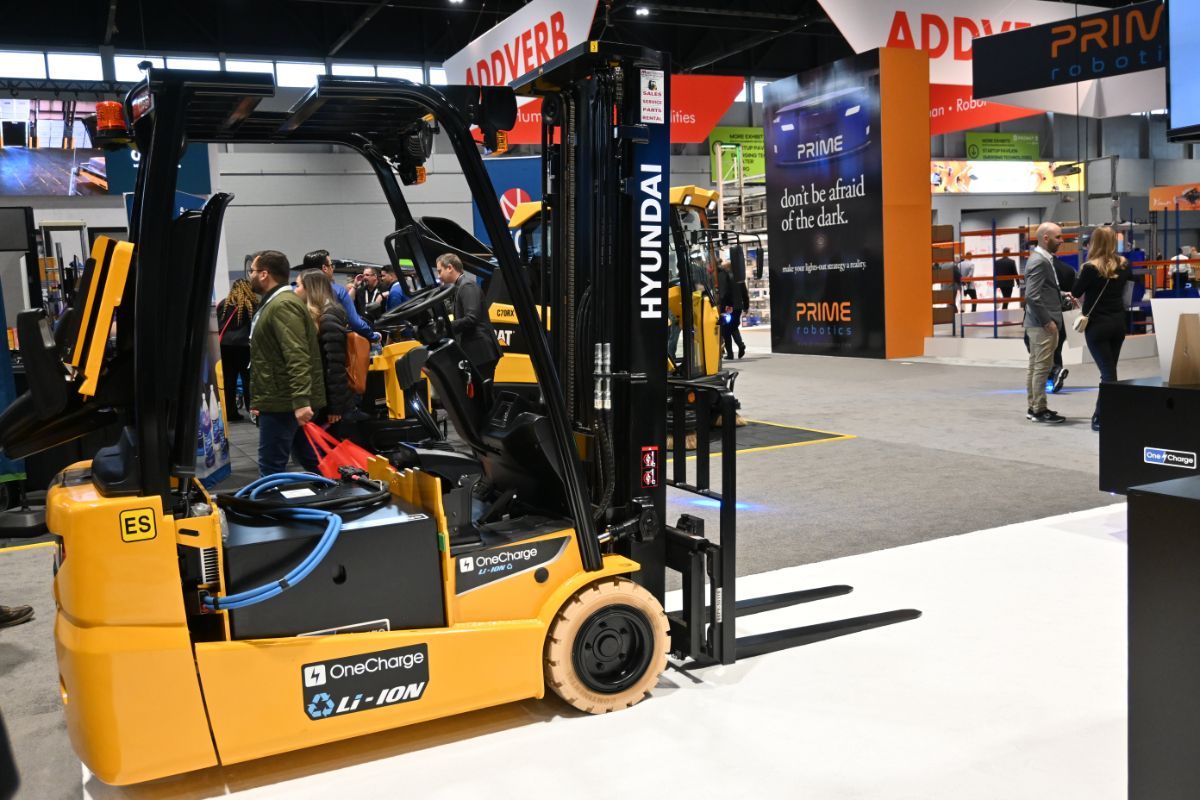
Use Energy-Efficient Lighting & Proper Ventilation
While not directly related to the forklift itself, operating in poorly lit or poorly ventilated environments can force operators to use headlights more often or overcompensate with power to manage visibility and heat. This creates unnecessary energy usage with the forklift and the warehouse itself.
Tip: Upgrade to LED lighting in warehouses and make sure there's adequate ventilation to reduce strain on operators and equipment.
Reduce Load-Carrying Trips
Unplanned or inefficient load movement increases energy usage. Forklifts that make multiple trips due to poor load planning consume more fuel and wear out faster.
Tip: Optimize picking and delivery routes. Use load planning software or warehouse management systems (WMS) to consolidate trips and reduce travel time. Encourage operators to maximize the efficiency of each run.
Consider Forklift Telematics & Fleet Management Systems
Modern forklift telematics offer detailed insights into energy use, operator behavior, and maintenance needs. These systems help identify inefficiencies and provide actionable data to reduce energy consumption.
Tip: Invest in fleet management solutions that integrate with your equipment. The ROI from energy savings, improved uptime, and extended equipment life often outweighs the initial investment.
Transition to Electric Forklifts Where Feasible
Electric forklifts are generally more energy-efficient than their gas or diesel counterparts, especially in indoor environments. They produce less heat, emit no exhaust fumes, and often cost less to operate over time.
Tip: Evaluate your operations for electrification opportunities. With advancements in battery technology, many electric models now match or exceed the performance of IC forklifts — even in outdoor or high-lift applications.
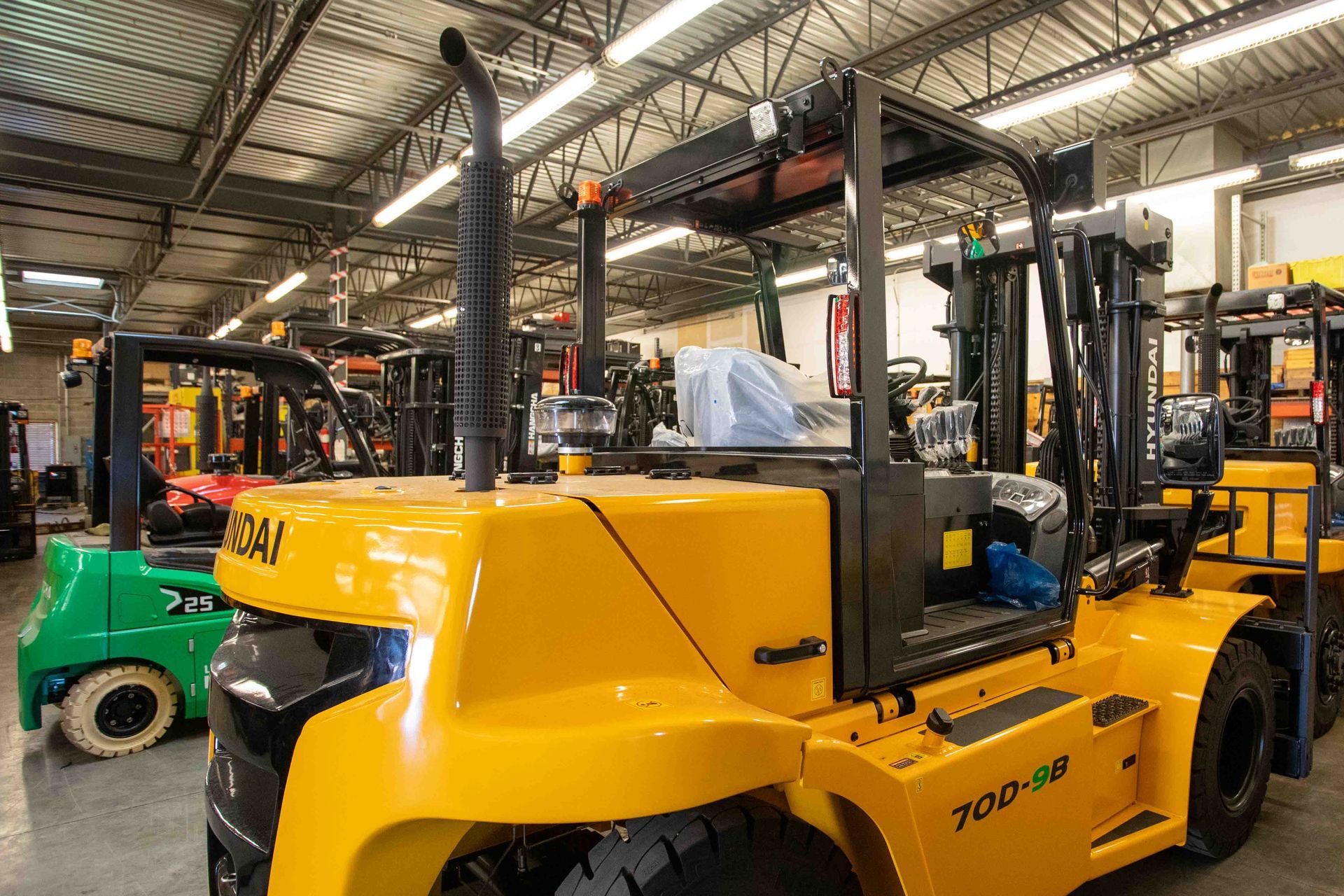
Work With Benco Industrial
Saving energy in forklift operations isn't just about cutting costs — it's about building a smarter, safer, and more sustainable operation.
By adopting even a few of these practices, facilities can see significant improvements in efficiency, reduced maintenance issues, and a lower environmental impact.
At Benco Industrial Equipment, we're here to help you find the exact solutions you need to keep your operation moving forward—whether that means forklifts, pallet jacks, order pickers, or a custom mix of equipment for your space and workload.
Contact us today to learn more!