Winter Warehouse Checklist
Autumn in the Midwest is a season of (often rapid) changes. Weather dips into colder temperatures and brings heavy precipitation before winter officially begins on December 21st. While you may feel that you have plenty of time before it arrives, it can sneak up quickly and leave you scrambling to figure out a game plan.
It’s never too early for warehouse owners, managers, and staff to prepare for colder temperatures, snow, ice, and potential issues they bring. Let’s go through a checklist of maintenance tasks.
Inspect and Maintain Heating Systems
Before the temperature drops, ensuring that your heating systems are in good working condition is crucial. A malfunctioning furnace or space heater can lead to discomfort and reduced productivity for your team. To avoid such issues:
- Schedule regular maintenance checks for your heating systems.
- Clean or replace filters to improve efficiency.
- Address any necessary repairs promptly to prevent breakdowns during the coldest days.
Proper Insulation
Proper insulation is critical in maintaining a comfortable and efficient warehouse during the winter. Insulation helps keep the cold air out and the warm air in. Here’s what you can do:
- Inspect your warehouse for gaps, cracks, or areas with poor insulation.
- Seal windows and doors to prevent drafts.
- Consider adding insulation to walls and the roof to further reduce heat loss.
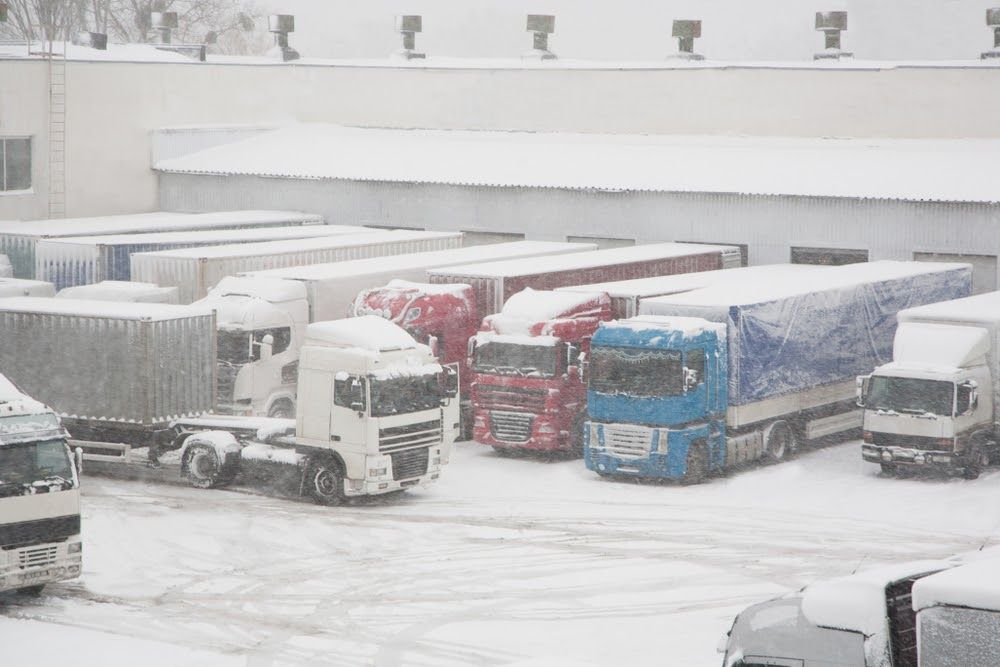
Snow and Ice Removal
The Midwest is known for its heavy snowfall and icy conditions. Failing to manage snow and ice around your warehouse can lead to accidents and disruptions in operations. To maintain safety:
- Arrange for snow and ice removal services to keep parking lots, walkways, and loading docks clear.
- Equip your team with shovels, salt, and snow blowers for immediate clearing when needed.
Floor Safety
Slippery warehouse floors are a significant safety hazard during the winter months. To prevent accidents:
- Ensure your warehouse floors are slip-resistant.
- Place anti-slip mats at entrances and high-traffic areas.
- Keep these areas dry by using absorbent materials.
Emergency Equipment
Winter can bring unexpected challenges and emergencies. Preparation is essential to be ready for any potential issues:
- Regularly inspect and maintain emergency equipment like fire extinguishers, first-aid kits, and emergency lighting.
- Train your staff on how to respond to winter-related emergencies, such as cold-related injuries or power outages.
Stock Up on Essentials
To keep your warehouse running smoothly, it’s essential to have a stockpile of winter essentials:
- Maintain ample salt, sand, and de-icing chemicals for snow and ice removal.
- Ensure your team can access warm clothing, gloves, and safety gear. You should keep extra parkas and gloves ready by the loading dock.
Weather Monitoring
Staying informed about weather conditions is crucial for making informed decisions. Consider:
- Investing in weather monitoring equipment to track temperature drops and incoming storms.
- Use this information to adjust work schedules, plan shipments, and prepare for adverse weather.
Scheduled Roof Inspections
A damaged or leaking roof can result in snow and water entering your warehouse, causing damage to inventory and equipment. To prevent this:
- Regularly inspect your warehouse’s roof for damage or leaks.
- Address any issues promptly to ensure your warehouse remains watertight.
Backup Power
Winter storms can lead to power outages, disrupting operations and compromising safety. Having backup power options is essential:
- Consider installing backup generators to provide electricity during power outages.
- Test these generators regularly to ensure they are in good working condition.
Employee Training
Your team is your most valuable asset, and their safety is paramount. Provide training on winter safety protocols:
- Educate employees on how to handle icy conditions and use cold-weather equipment safely.
- Foster a culture of safety and vigilance throughout the winter months.
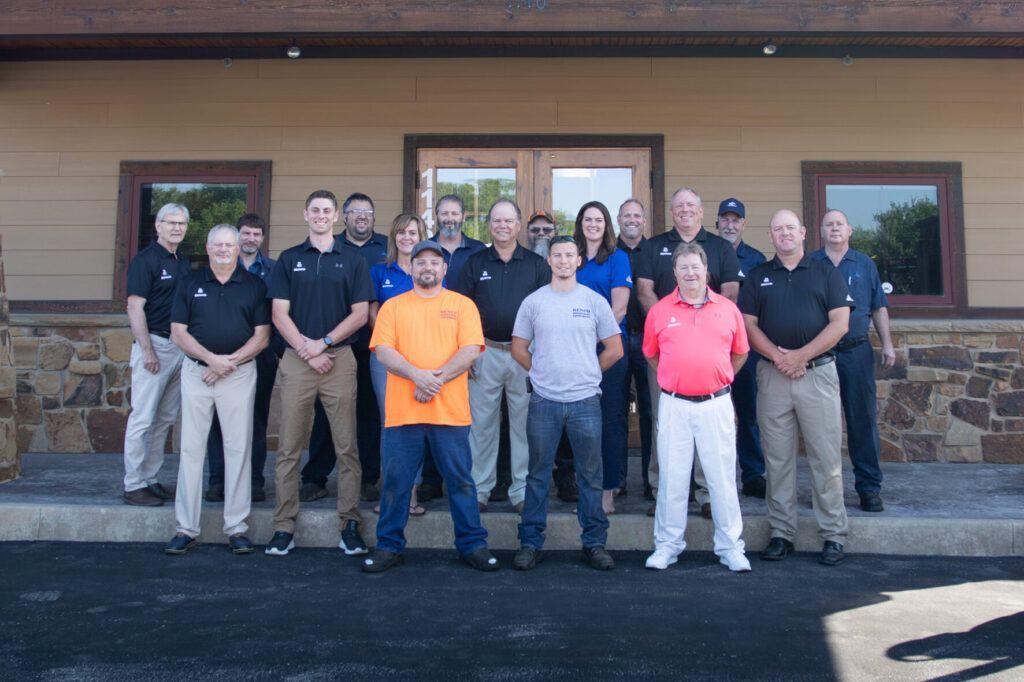
Work With Benco Industrial Equipment
Preparing your warehouse for winter in the Midwest is not just a matter of convenience but safety and efficiency. By following these ten essential tips, you can ensure that your warehouse remains a safe and productive environment during the coldest months of the year. Proper planning and preparation will protect your team and business from winter challenges.
Here at Benco Industrial Equipment, we know the ins and outs of the materials handling industry and can help you choose the best equipment for your warehouse or project. We have both electric and IC forklifts ready to buy or rent. Looking for legless stackers, straddle stackers, work assist forklifts, or reach stackers? We’ve got them. We’ll keep your warehouse clean with floor sweepers, scrubbers, industrial fans, and other equipment to help your warehouse succeed. Get in touch with us today!
The post Winter Warehouse Checklist appeared first on Benco Industrial Equipment.